塑膠射出(Injection Molding)是一種廣泛應用於現代製造業的高效加工技術,特別是在塑料製品的生產過程中。
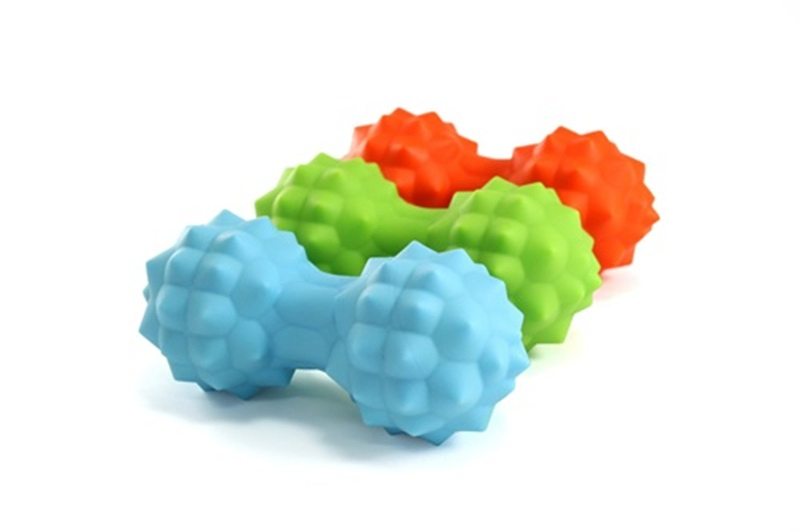
進揚企業有限公司
塑膠射出、開發各類塑膠射出、TPR軟質塑膠
TEL: 04-7523565 FAX:04-7626987
彰化市彰馬路345號
塑膠射出:現代製造的核心技術
塑膠射出(Injection Molding)是一種廣泛應用於現代製造業的高效加工技術,特別是在塑料製品的生產過程中。這一技術通過將熔融塑料注射進入模具中,經過冷卻後成型,從而製造出各種塑料零件。塑膠射出以其高精度、高效率和低成本的特點,成為許多行業中關鍵的生產工藝,廣泛應用於汽車、電子、消費品、醫療器械、家電等領域。
塑膠射出的基本原理
塑膠射出的基本原理是將塑料原料加熱至熔融狀態,再通過注射機將熔融的塑料快速注入模具中,模具中的空腔會根據設計的要求,塑形並冷卻成型。這一過程需要精確的控制熔融塑料的溫度、壓力、注射速度等參數,以確保產品的品質和一致性。
具體流程可以分為以下幾個主要步驟:
塑料原料準備:塑料顆粒(或粉末)經過乾燥處理,然後進入注射機的料斗中。
加熱與熔融:塑料原料在注射機的螺桿作用下被加熱至熔融狀態,達到合適的流動性。
注射到模具中:熔融塑料通過高壓被迅速注射進入模具的空腔中,並完全充滿模具,形成所需形狀。
冷卻與固化:注射後,塑料在模具內冷卻,並固化為塑料產品。冷卻時間取決於材料特性和產品的複雜程度。
脫模:經過冷卻固化後,模具打開,成型的塑料零件被取出,完成生產。
塑膠射出的優勢
高效率:塑膠射出成型的生產速度非常快,尤其適合大規模生產。一次模具注塑可以批量生產大量相同或相似的塑料零件,並且每個零件的尺寸精度非常高。
高精度:現代塑膠射出技術可以實現極高的精度,能夠生產出複雜形狀且尺寸一致的塑料部件。這對於對精度要求高的領域,如電子產品和醫療器械尤為重要。
材料利用率高:在塑膠射出過程中,塑料原料被完全利用,浪費較少。同時,生產過程中的多餘塑料(如邊角料)可以回收再利用,進一步提高了資源的利用效率。
適應性強:塑膠射出成型技術可使用多種不同的塑料材料,包括熱塑性塑料、熱固性塑料等。這使得其能夠應用於各種行業和需求中,從日常用品到高精度的工業零件均能製作。
複雜結構的製造能力:塑膠射出可以生產出非常複雜的塑料部件,這些部件可能包括細小的孔洞、凹槽、卡扣等結構,這些結構在傳統的加工方式中往往難以實現。
塑膠射出的應用領域
塑膠射出技術的應用範圍非常廣泛,涵蓋了幾乎所有使用塑料材料的行業。以下是一些典型的應用領域:
汽車行業:汽車零部件的生產中,許多內外部零件(如儀表板、內飾件、外殼、固定扣件等)都使用塑膠射出技術。這些部件需要具備高強度、輕量化和耐用性,並且能夠承受高溫和外界衝擊,塑膠射出能夠提供這些需求。
電子行業:電子產品中的外殼、面板、內部支架等許多零件都使用塑膠射出成型。隨著消費電子產品的日益輕薄化、精密化,射出成型技術在精密部件生產中的應用越來越重要。
醫療器械:醫療領域中的塑料部件要求高精度和高穩定性,塑膠射出技術能夠提供這些要求。許多一次性使用的醫療器械,如注射器、醫用容器等,都是通過塑膠射出成型製造的。
消費品:從食品包裝、日用化妝品包裝到玩具、家居用品,塑膠射出在消費品領域的應用無處不在。由於塑料材質輕便且具有優異的加工性能,塑膠射出在消費品行業中發揮了關鍵作用。
包裝行業:塑料包裝材料、瓶蓋、容器等通常使用塑膠射出技術生產。這些包裝材料需要具備強度、耐用性以及良好的密封性,射出成型能夠滿足這些要求。
塑膠射出的挑戰與未來
儘管塑膠射出技術在現代製造中具有極高的應用價值,但也面臨一些挑戰。首先,模具的製造成本較高,尤其是對於複雜設計的零件,這使得小批量生產的成本較高。其次,不同塑料材料的選擇會影響到成型過程的控制,對材料的選擇和使用具有較高的要求。
未來,隨著技術的發展,塑膠射出將不斷優化,特別是在提高生產效率、降低成本以及進一步提高精度方面。此外,與其他技術的結合,如3D打印和智能製造,也將成為塑膠射出技術未來發展的重要方向。
結論
塑膠射出作為一種高效且靈活的製造工藝,已經在現代製造業中發揮了至關重要的作用。它不僅能夠大規模、高精度地生產各種塑料零件,還具備極高的生產效率和較低的生產成本。隨著技術的進步,塑膠射出將在更多領域中發揮其潛力,推動各行各業的創新與發展。
塑膠射出的創新與發展趨勢
隨著市場需求的不斷增長以及製造工藝的進步,塑膠射出技術也在不斷創新與發展。以下是塑膠射出未來的一些主要發展趨勢:
精密化與微型化
隨著電子產品、醫療器械等領域對精度要求的提高,塑膠射出技術也逐漸向更高的精度和微型化方向發展。微型射出成型(Micro Injection Molding)技術允許在極小的範圍內進行精確製造,這對於製造極細小、複雜的塑料部件至關重要。例如,許多穿戴式設備和微型電子元件都依賴於此技術。
多材料射出成型
傳統的塑膠射出技術主要應用於單一材料的塑料部件生產,而隨著需求的多樣化,多材料射出成型技術逐漸興起。這一技術通過在同一模具中同時注射多種不同材料的塑料,實現具有不同物理性能(如硬度、柔韌性、抗氧化等)的部件。一些現代消費品和電子設備中,已經開始應用此技術,實現了複雜部件的多功能化。
生物降解塑料的應用
隨著環保意識的提升,許多行業正在尋求可持續發展的替代品。生物降解塑料成為了一個重要的研究方向。塑膠射出技術也開始逐步應用在這類可降解材料的加工中,以減少塑料垃圾對環境的影響。雖然目前生物降解塑料的性能仍在不斷提升中,但隨著技術的進步,這一領域將在未來發揮更大作用。
高效率與自動化
隨著製造業對生產效率的要求不斷提高,塑膠射出行業的自動化程度也在逐步提高。從原料處理、注塑機操作到產品檢查,現代射出成型生產線已經開始引入大量自動化設備,這些設備能夠實現生產過程的高度自動化,顯著提高產能並減少人工操作,提高生產效率。
智能化與大數據應用
隨著工業4.0的推動,塑膠射出行業正在逐步實現智能化和數字化。智能塑膠射出機和生產線可以通過大數據分析來監控生產過程,預測可能出現的問題,並且即時調整生產參數以保證產品品質。這不僅提高了生產的精確性,還能在生產過程中實現優化,從而有效降低浪費並提高能效。
3D打印與塑膠射出技術結合
3D打印技術在快速原型製作方面的優勢無可置疑,但在量產方面仍然存在一些局限。隨著3D打印技術和塑膠射出技術的結合,將能夠實現更高效的生產過程。例如,可以利用3D打印製作射出模具原型,並通過傳統射出成型進行大規模生產,從而縮短產品開發時間,降低成本,並保持量產所需的精度。
塑膠射出的挑戰
儘管塑膠射出技術在許多領域都具有不可替代的重要地位,但在其發展過程中也面臨著一些挑戰:
原材料價格波動
塑膠射出生產所需的塑料原料價格存在波動,這對製造商的成本管理構成挑戰。尤其是一些特殊材料(如工程塑料、複合材料等)的價格變動會直接影響最終產品的成本。
模具製作與維護成本
雖然塑膠射出成型技術本身具有較高的生產效率,但模具的製作成本卻相對較高,尤其是對於複雜或精密部件的生產。模具的設計和製作過程需要大量的專業知識,並且隨著生產規模的增大,模具的維護和更換也是一項重要的成本支出。
環保與可持續發展要求
雖然塑膠射出技術本身不會對環境造成直接危害,但由於塑料垃圾的日益增加,環保法規逐漸收緊,對塑膠製品的回收利用、再生利用提出了更高要求。因此,未來塑膠射出技術需要更多地關注環保材料的應用以及生產過程中的能效和資源利用率。
塑料材料的多樣性與適應性
雖然塑膠射出能夠處理各種塑料材料,但某些高性能塑料材料(如超高分子量聚乙烯、聚酰亞胺等)在射出過程中的流動性差或易發生分解,這給技術操作帶來了困難。如何使塑膠射出工藝更好地適應這些高性能材料,將是未來研究的重點之一。
結論
塑膠射出作為現代製造業中一項不可或缺的生產工藝,隨著技術的發展,正在不斷創新與進步。從精度的提升到生物降解材料的應用,再到自動化和智能化的發展,塑膠射出技術未來的發展潛力無限。儘管面臨一些挑戰,但隨著新材料的出現、製程的優化以及環保需求的日益增長,塑膠射出技術必將在全球製造業中發揮更加重要的作用,並推動各行各業的可持續發展。
塑膠射出成型製造:現代製造業的核心技術
塑膠射出成型製造是一種高效且多用途的加工技術,廣泛應用於汽車、電子、醫療、日用品等各個行業。它以其高效率、精確性和靈活性,成為現代塑膠產品製造的核心技術。本文將從塑膠射出的原理、製程、應用及未來發展等方面進行詳細探討。
一、塑膠射出成型的基本原理
塑膠射出成型是一種將熱塑性或熱固性塑膠材料加熱至熔融狀態,然後利用高壓將其注入模具腔內,冷卻後形成所需產品的製程。其基本流程包括以下幾個步驟:
加熱熔融
塑膠原料在射出機的加熱筒內被加熱至熔融狀態。
注入模具
熔融塑膠在高壓驅動下通過噴嘴注入模具腔,填滿整個模腔。
冷卻與固化
塑膠在模具內冷卻固化,形成穩定的結構。
開模取出
固化後的塑膠件被取出模具,完成一次成型。
二、塑膠射出成型製造的優勢
塑膠射出成型技術之所以能在製造業中佔據重要地位,主要得益於其多方面的優勢:
高效率
一次射出即可生產多個相同或不同的零件,生產週期短,適合大批量製造。
高精度
模具設計的精確性可確保產品尺寸的穩定性,適用於製造精密零件。
多樣化材料選擇
可使用多種塑膠材料,包括ABS、PP、PE、PC、PVC等,滿足不同性能需求。
設計靈活性
模具設計靈活,可實現複雜的幾何結構,並滿足產品輕量化要求。
低廢料率
塑膠射出成型的材料利用率高,邊角料可回收再利用,環保且經濟。
三、塑膠射出成型製程的關鍵因素
塑膠射出成型的成功與否取決於多個製程因素,包括:
溫度控制
熔融溫度需根據塑膠材料的特性進行調整,過高或過低都可能影響產品質量。
射出壓力
射出壓力需確保熔融塑膠能填滿模具,過低可能導致產品缺陷。
冷卻時間
冷卻過程影響產品的尺寸穩定性和外觀質量,過短可能導致翹曲或變形。
模具設計
模具的結構設計直接決定產品的形狀、尺寸及功能。
四、塑膠射出成型的應用領域
塑膠射出成型因其適應性強,在眾多行業中發揮著不可或缺的作用:
汽車製造
生產汽車零件如儀表板、保險桿和內飾件,滿足輕量化與耐用性需求。
電子產品
用於製造手機外殼、鍵盤、連接器等高精度零件。
醫療器材
生產一次性注射器、試管及醫療設備外殼,符合高潔淨度要求。
日用品
廣泛應用於家庭用品、包裝盒、玩具等產品的製造。
五、塑膠射出成型的挑戰與解決方案
雖然塑膠射出成型技術具有眾多優勢,但也面臨一些挑戰,如:
模具成本高
高精度模具設計與製造成本昂貴,適合大批量生產的產品。
解決方案:採用快速成型技術或模具共享策略以降低成本。
製程複雜
對溫度、壓力及冷卻等參數要求高,稍有不慎可能導致產品缺陷。
解決方案:引入智能控制系統,精確監控並優化製程。
環境壓力
塑膠材料的使用帶來廢棄物問題。
解決方案:採用可降解塑膠材料,並加強回收與再利用。
六、塑膠射出成型的未來發展趨勢
隨著技術進步和市場需求的變化,塑膠射出成型正朝著以下方向發展:
智能化生產
結合物聯網與自動化設備,實現全自動監控與操作,提升生產效率與精度。
環保材料應用
開發生物降解塑膠材料,減少對環境的影響。
微型化與精密化
滿足醫療、電子等行業對微型零件的需求,進一步提升技術精度。
快速成型技術
縮短模具製造時間,加速產品開發週期,滿足市場快速變化需求。
結語
塑膠射出成型製造技術以其高效率、高精度及靈活性,成為現代製造業中不可或缺的核心技術。隨著智能化、環保化和精密化的發展,塑膠射出成型的應用領域將持續拓展,為各行各業提供更加優質的解決方案,推動製造業的創新與進步。
以下是關於塑膠射出成型製造的更多細節,補充行業應用與技術發展:
七、塑膠射出成型製造的專業設備
塑膠射出成型過程依賴專業設備,主要包括射出機、模具和輔助設備,每個部分都對最終產品的質量和效率至關重要。
射出機
分類:根據驅動方式,射出機可分為液壓式、全電動式和混合式。
特點:全電動射出機以精度高、能耗低著稱,適合製造高精度產品。
模具
材質:模具一般使用鋼材或鋁材製成,鋼材適用於大批量生產,鋁材則適合小批量與快速成型。
功能:模具結構包括定模、動模、澆口系統和冷卻系統,每一部分都影響產品的形狀和質量。
輔助設備
溫控機:控制模具溫度,確保熔融塑膠的流動性和產品固化均勻。
乾燥機:在成型前乾燥塑膠顆粒,避免水分影響產品質量。
八、塑膠射出成型的行業應用進一步擴展
航空航太
射出成型技術可生產輕量化、耐高溫的塑膠零件,如飛機內部裝飾件。
家電行業
製造如電視機外殼、洗衣機零件等耐用且美觀的塑膠部件。
包裝行業
使用透明或彩色塑膠製成食品容器、化妝品瓶蓋等,兼具實用性和吸引力。
運動用品
塑膠射出成型適用於製造如頭盔、護膝、運動鞋底等安全且功能性的部件。
九、塑膠射出成型中的質量控制
為確保產品達到設計標準,質量控制在塑膠射出成型過程中尤為重要。
檢測設備
使用CMM(坐標測量機)檢查產品的尺寸精度。
使用X光或CT掃描技術檢測產品內部結構。
缺陷預防
通過調整射出壓力和溫度,避免短射或氣泡等常見問題。
優化模具設計,減少翹曲或表面缺陷。
流程監控
使用智能監控系統實時監控製程參數,提前發現並解決潛在問題。
十、塑膠射出成型與其他加工技術的比較
塑膠射出成型與其他加工技術相比,具有獨特的優勢和適用性。
與吹塑成型相比
吹塑適合中空產品如瓶子,而射出成型適合製造結構複雜的實心產品。
與3D列印相比
3D列印適合原型製作和小批量生產,而射出成型更適合大批量且成本敏感的製造。
與擠出成型相比
擠出成型適合製造管狀或片狀產品,而射出成型適合多樣化零件。
十一、塑膠射出成型的環保挑戰與解決方案
挑戰
塑膠廢棄物對環境的影響。
能源消耗高。
解決方案
採用可降解塑膠材料,如PLA(聚乳酸)。
開發節能型射出設備,降低製造過程中的能源使用。
推廣塑膠回收技術,實現材料的循環利用。
十二、塑膠射出成型的未來技術展望
數位化與智能製造
通過人工智慧和大數據分析,實現射出成型全過程的數位化管理。
增強功能性材料的應用
開發具有特殊性能的塑膠材料,如導電性、高強度或自修復性材料。
模具設計創新
採用模流分析軟體優化模具設計,提高產品質量與成型效率。
多材料成型技術
實現多種塑膠材料的混合成型,滿足產品多功能需求。
結語
塑膠射出成型製造是現代製造業的支柱技術之一,憑藉其高效性、靈活性和成本效益,在全球範圍內被廣泛應用。隨著智能化、生態化和精密化的推進,塑膠射出成型將進一步突破技術界限,為製造業的可持續發展和創新升級提供無限可能。
檔案下載:塑膠射出成型製造
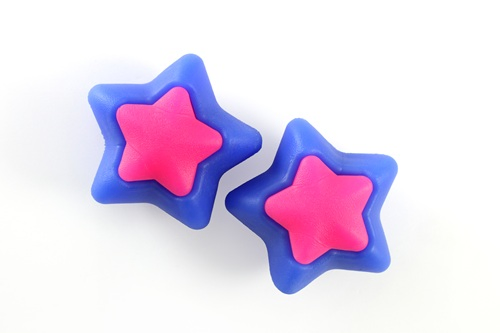
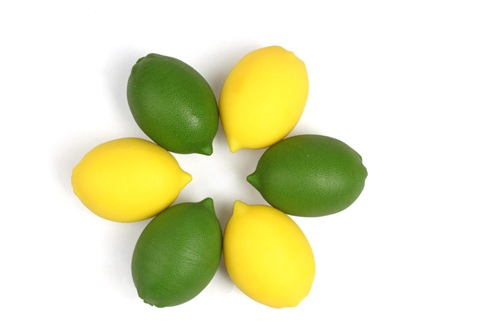
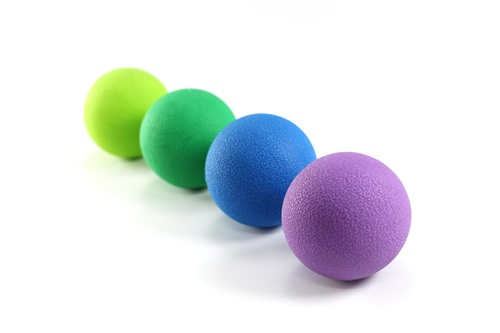
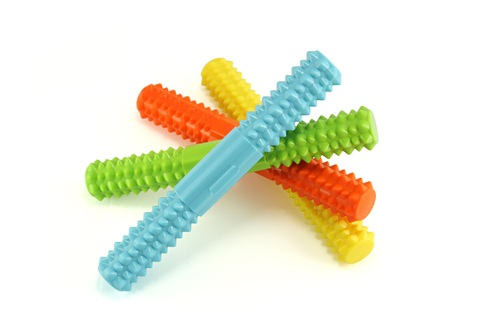
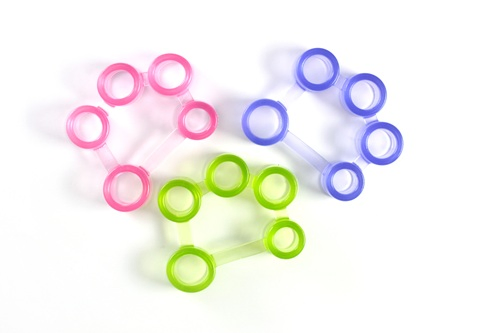